Welding is a critical process in industries like construction, oil and gas, manufacturing, and shipbuilding. The choice between using welding rotators or manual welding can significantly impact the efficiency, cost, and quality of your operations. While manual welding has been a staple for years, welding rotators are becoming increasingly popular for their ability to handle heavy and cylindrical workpieces with precision.
In this blog, we’ll compare welding rotators and manual welding to help you decide which is better suited for your businesses in the UAE.
What Is Manual Welding?
Manual welding is a traditional method where a welder performs the welding process by hand, controlling the heat, speed, and movement. This method requires a skilled welder who can manually adjust the position of the workpiece to achieve a continuous and precise weld.
What Are Welding Rotators?
Welding rotators in UAE are mechanical devices designed to rotate cylindrical or round workpieces during the welding process. These machines automate the rotation, allowing welders to focus on the welding itself rather than adjusting the position of the workpiece.
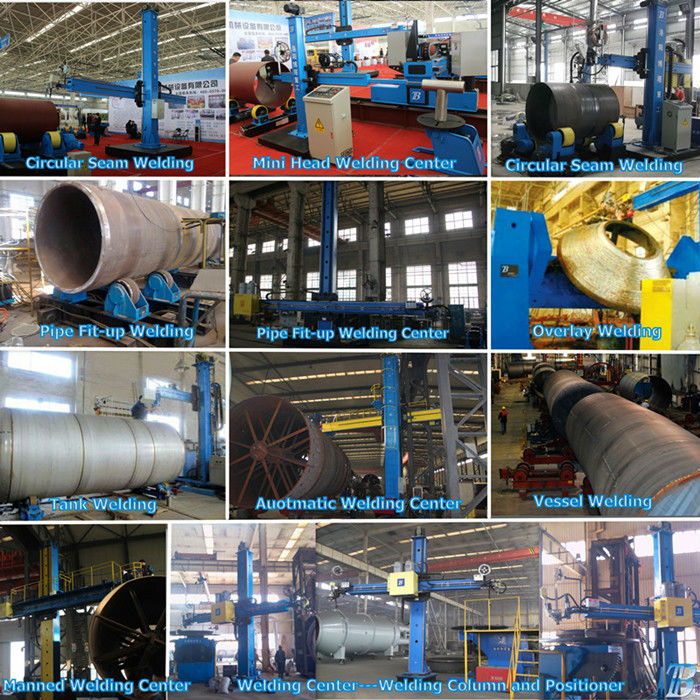
Comparison: Welding Rotators vs. Manual Welding
1. Efficiency
- Manual Welding:
Manual welding is time-consuming, especially for large or heavy workpieces that require repositioning. Welders often need to pause and adjust the object, which can slow down the process. - Welding Rotators:
Welding rotators automate the rotation of workpieces, significantly reducing downtime. With consistent rotation, welders can focus solely on welding, completing projects faster and more efficiently.
2. Weld Quality
- Manual Welding:
The quality of manual welding depends heavily on the welder’s skill. It can be difficult to maintain a consistent weld on a cylindrical object, which might result in irregularities in the weld bead. - Welding Rotators:
By ensuring constant and steady rotation, rotators enable accurate and consistent welds. This is particularly important in industries where weld integrity and appearance are crucial.
3. Safety
- Manual Welding:
Welding large and heavy workpieces manually involves risks such as strain injuries, accidental slips, and potential equipment failures. Welders may also need to work in awkward positions, increasing the chance of injury. - Welding Rotators:
By removing the need for physical lifting or moving heavy objects, welding rotators increase safety. The workpiece is securely held and rotated automatically, reducing the risk of accidents.
4. Cost
- Manual Welding:
While the initial investment for manual welding equipment is lower, labor costs can add up over time, especially for large-scale or repetitive projects. The potential for errors and rework also increases overall expenses. - Welding Rotators:
Welding rotators require a higher initial investment but offer long-term cost savings. They cut down on material waste, labor expenses, and the possibility of rework because of subpar weld quality.
5. Versatility
- Manual Welding:
Manual welding is versatile in terms of handling small and irregularly shaped objects. Welders can adapt to different angles and positions as needed. - Welding Rotators:
Welding rotators excel at handling cylindrical and heavy workpieces. However, they are not ideal for small, intricate, or irregular shapes. Self-aligning rotators offer some flexibility by accommodating workpieces of varying diameters.
6. Scalability and Automation
- Manual Welding:
Manual welding is labor-intensive and difficult to scale for large projects. It also lacks compatibility with automation technologies. - Welding Rotators:
Welding rotators are compatible with robotic welding systems, enabling automation and scalability. They are therefore perfect for sectors requiring a lot of manufacturing.
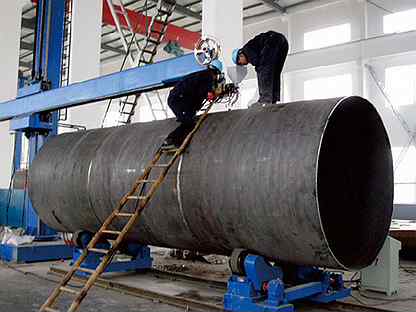
Which Is the Right Fit for Your Business?
The choice between manual welding and welding rotators in UAE depends on several factors, including:
- Budget: Consider the initial cost of equipment and ongoing maintenance expenses.
- Volume and Complexity of Work: High-volume, repetitive tasks are ideal for rotators, while low-volume, customized work may be better suited for manual welding.
- Skill Level of Welders: Rotators can help less experienced welders achieve consistent results, while skilled welders may prefer the flexibility of manual welding.
- Quality Standards: If high-quality, consistent welds are a priority, welding rotators can be a valuable investment.
- Ergonomics: To reduce the risk of injuries, consider the ergonomic benefits of welding rotators.
Conclusion
While manual welding remains a reliable method for smaller, more intricate projects, welding rotators provide unmatched benefits for large-scale operations. They improve efficiency, enhance weld quality, ensure safety, and pave the way for automation.
For businesses in the UAE looking to stay competitive and optimize their welding processes, investing in welding rotators is a smart and forward-thinking choice. Here, Rockwood is the right choice we consider the long-term benefits, and make an informed decision to ensure your welding operations run smoothly and cost-effectively.
For any enquiry Call us at +971 4 8816636 or visit our website at Rockwood Welding Automation to learn more.