In this fast-paced industrial sector, speed, accuracy and reliability are key in selecting the right welding technology. As industries evolve, laser welding machines have become an effective solution for any organization in search of improved efficiency without compromising product quality. For your welding equipment supplier in UAE, look no further; Rockwood Welding Automation is a trusted provider of the latest welding solutions.
This blog takes a look at the top five reasons why laser welding is the smart choice for industrial applications and how it can change your welding processes for good.
1. Superior Precision and Accuracy
High precision is one of the best features of the laser welding process. Unlike traditional welding methods that rely on bulky electrodes or gas torches, laser welding machines in UAE use a highly concentrated laser beam that allows for:
- Minimal heat-affected zones – reducing material distortion
- Exceptional accuracy – perfect for delicate or intricate welding tasks
- Seamless welds – ensuring strong and flawless joints
For critical industries like automotive, aerospace, and electronics, laser welding gives precision that conventional welding cannot hope to achieve.
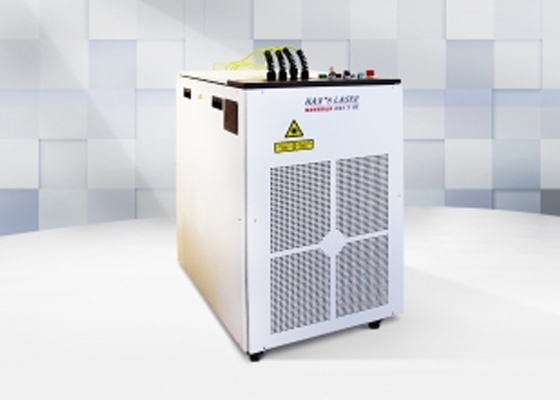
2. Increased Speed and Efficiency
As industrial applications operate on speed and, at the same time, demand quality, conventional welding often elongates this process, leading to higher labor costs and production delays. Laser welding, however, offers:
- Faster welding speeds – completing tasks in a fraction of the time
- Reduced post-processing – minimal grinding, sanding, or polishing required
- Automated operation – All welding activities can be automated in order to improve working efficiency and minimize or eliminate human intervention.
By associating with a welding equipment supplier like Rockwood Welding Automation, you will now equip your facility with laser welding machines that improve productivity and significantly reduce downtime.
3. Versatility Across Industries and Materials
Laser welding is an incredibly versatile process, which allows for a wide number of fields of applications in the industry. Whether you’re working with steel, aluminum, titanium, or even dissimilar metals, laser welding provides joints which are strong and durable. Key industries benefiting from laser welding include:
- Automotive manufacturing – for body panels, batteries, and fuel injectors
- Aerospace – ensuring lightweight yet durable component connections
- Medical devices – for high-precision surgical tools and implants
- Electronics – micro-welding for circuit boards and delicate components
The capability of welding different materials with no distortion or very little makes laser welding an indispensable welding mode in any modern manufacturing process.
4. Cost-Effective and Energy-Efficient
There is often a high amount of energy consumption, material wastage, and labor costs associated with traditional welding procedures. In contrast, laser welding helps reduce operational expenses by:
- Minimizing consumable usage – no need for electrodes, filler materials, or shielding gases
- Reducing material waste – due to its pinpoint accuracy and minimal distortion
- Lowering energy consumption – laser welding requires significantly less power than conventional methods
While this may mean a significant upfront investment for a manufacturer, purchasing a laser welding machine is an economical solution that pays off in the long run.
5. High-Quality, Consistent Welds
Quality and consistency are a no-questions-asked demand in industrial applications. Traditional welding processes have countless inconsistencies, contributing to variances at the weld, largely attributed to human error and fluctuations in material properties. However, laser welding provides:
- Flawless, repeatable welds – ensuring uniformity across production batches
- Stronger weld integrity – reducing the risk of weak joints or defects
- Minimal oxidation or contamination – due to its non-contact, high-purity process
For those businesses that are in need of high-performance welding solutions, Rockwood Welding Automation provides high-tech laser welding equipment that ensures superior quality with every weld.
Conclusion
As industrial applications demand greater efficiency, precision, and cost-effectiveness, laser welding has become the preferred choice for manufacturers worldwide. Having said that, whether you work in automotive, aerospace, medical, or electronics manufacturing, integrated laser welding machines can improve productivity and weld quality.
If you’re looking for a reliable welding equipment supplier in UAE, Rockwood Welding Automation provides top-of-the-line laser welding solutions tailored to meet your industry’s needs. Upgrade your welding processes today and experience the benefits of speed, accuracy, versatility, and cost savings with laser welding.
For further reading, click: What Is MMA (Manual Metal Arc) Welding? All You Need To Know